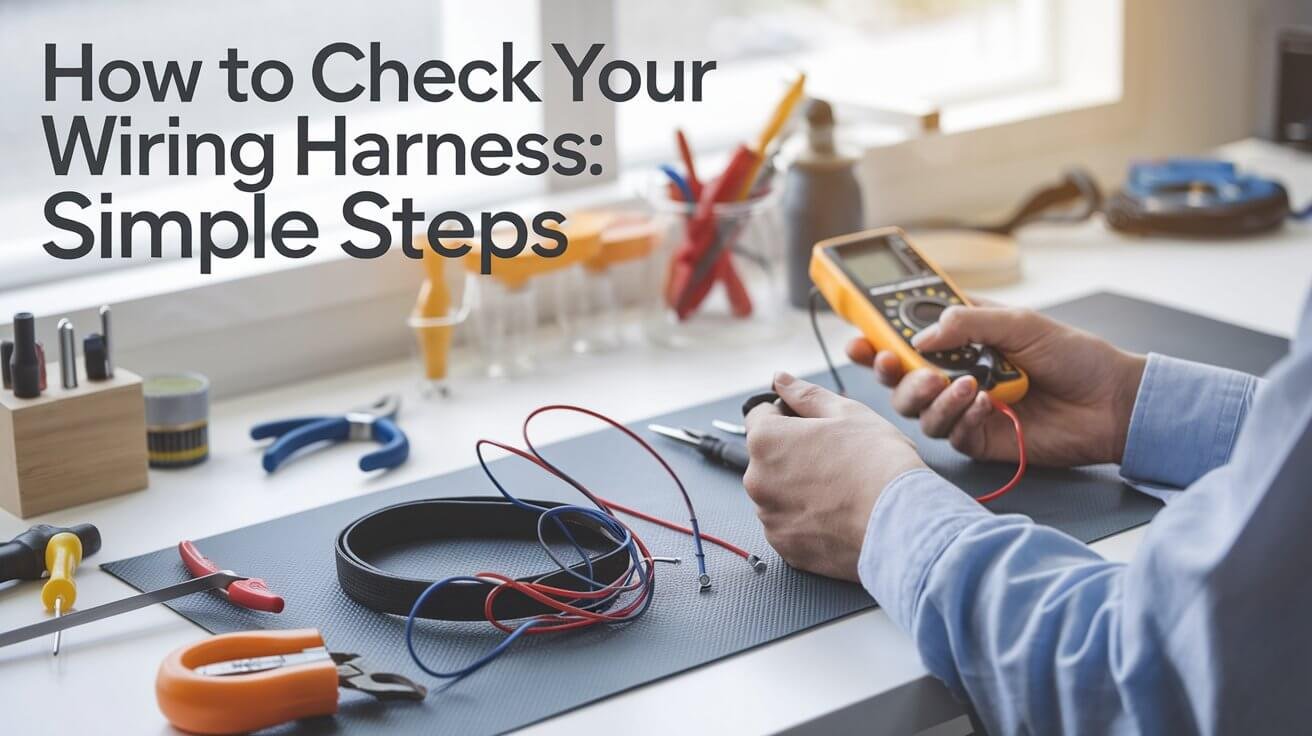
We know how key a good wiring harness is for your car. For years, we’ve used many tests to check electrical circuits. Load testing has been a mainstay for over 20 years. It helps us spot problems and fix them quickly.
Inspecting wiring harnesses starts with disconnecting both ends. We use special tools, like those from AES Wave, to check each wire. This way, we can do several tests at once, saving time. We also use tools like the Load Pro or even headlight bulbs to check the circuit’s health.
Our team has lots of experience in this area. Many have found that using bulbs for testing is as good as modern tools. Our aim is to give you quick and accurate checks, making sure your car’s electrical system works right.
Key Takeaways
- Wiring harness inspection involves disconnecting both ends, back probing, and using a light bulb to test for shorts, voltage drops, and circuit integrity.
- Load testing is a reliable way to verify wire integrity and identify issues that simple continuity tests might miss.
- Experienced technicians utilize a variety of tools, including load testing equipment and standard headlight bulbs, to diagnose electrical problems efficiently.
- Understanding circuit design is crucial for ruling out certain wiring issues and streamlining the troubleshooting process.
- Using the right tools, such as multimeters and power probes, can save time and reduce guesswork in diagnosing automotive electrical problems.
Fundamentals of Wiring Harness Testing
Testing a wiring harness is key to keeping electrical systems running smoothly. To do this, we need to know how to test for continuity, check for wire damage, and verify connector integrity. Let’s start with the basics of wiring harness testing.
Basic Circuit Components
A wiring harness has many parts, like wires, connectors, terminals, and splices. We must test each part well to find any problems. This includes checking for resistance faults, short circuits, or connections that don’t always work.
Testing Equipment Requirements
To test a wiring harness fully, we need special tools. These include digital multimeters, test lights, and harness testing tools. These help us measure voltage, current, resistance, and continuity. They also help find issues in the wiring.
Safety Precautions Before Testing
- Disconnect the battery to prevent accidental shorts or electrical shocks.
- Wear appropriate personal protective equipment (PPE), such as insulated gloves and safety glasses.
- Ensure a well-lit and organized work area to minimize the risk of mistakes or accidents.
- Follow manufacturer’s instructions and industry best practices for safe testing procedures.
Knowing the parts of a wiring harness, using the right tools, and keeping safety first are crucial. This way, we can test for continuity, check wire damage, and verify connector integrity. This ensures electrical systems work well and reliably.
Common Wiring Harness Problems and Symptoms
Vehicles today rely a lot on their electrical systems. Knowing the common problems and symptoms of wiring harnesses is key for fixing and keeping them running well. These parts can face many issues, like short circuits, open circuits, and faulty connections.
Wiring harnesses often fail due to their tough environment. Extreme temperatures, road bumps, humidity, and vibrations can damage them. This can cause problems like malfunctioning accessories, dead batteries, and engine issues.
Wiring harness failures can also mess up data transmission. This affects many electronic systems and gadgets in the car. Regular checks and careful handling during installation or replacement are vital to avoid these issues.
To fix wiring harness problems, a detailed testing and diagnosis process is needed. This includes looking at the wiring, taking electrical measurements, and testing the load. It helps find the cause, whether it’s a manufacturing flaw, wear and tear, or a problem with nearby parts.
Common Wiring Harness Problems | Potential Symptoms |
---|---|
Short circuits | Blown fuses, electrical component malfunctions |
Open circuits | Dim lights, non-functioning electrical components |
High resistance connections | Intermittent operation, electrical system issues |
Intermittent faults | Unpredictable electrical behavior, data transmission errors |
Understanding common wiring harness problems and their symptoms helps car owners and mechanics fix electrical issues. This ensures the vehicle runs well and its electrical parts last longer.
Essential Tools for Harness Diagnostics
To do a good job in automotive wiring diagnostics, you need the right tools. A few key instruments are crucial for finding problems, checking connections, and making sure wiring is good. These tools help us keep our vehicle’s wiring in top shape.
Digital Multimeters and Their Uses
A digital multimeter is a must-have for car wiring checks. It lets us measure voltage, resistance, and continuity in different circuits. With a multimeter, we can spot issues in the wiring and find electrical problems fast.
Test Lights and Load Testing Equipment
Test lights and load testers are also key for diagnosing harnesses. Test lights show if power and ground are present in a circuit. Load testers, like headlight bulbs, help us test how the electrical system works under real conditions. They help us find short circuits or voltage drops.
Specialized Harness Testing Tools
For detailed car wiring checks, specialized tools are a big help. Tools like CableEye offer advanced testing features. They can measure resistance, set dual thresholds, and find intermittent faults. These tools let us explore the electrical system’s details and make sure it’s working right.
Having the right tools is key for car wiring diagnostics and electrical system checks. With digital multimeters, test lights, load testers, and specialized tools, we can find and fix many wiring issues. This makes our vehicles more reliable and our drives better.
How To Check Your Wiring Harness
Keeping your vehicle’s wiring harness in good shape is key for reliable electrical systems. We’ll show you how to inspect your wiring harness step by step. This includes visual checks, continuity tests, and load tests. These steps help you find and fix any wiring harness inspection, electrical system troubleshooting, or automotive wiring diagnostics problems.
Begin with a visual check of the wiring harness. Look for any damage like cracks, frays, or exposed wires. Also, check for wear and tear, loose, or corroded connections. This first look can help you find potential issues before you do more detailed tests.
Then, use a digital multimeter to check for continuity and resistance. Use the vehicle’s wiring diagrams to test the right circuits. Aim for a 0 ohm reading to show a good connection. Any reading over 1.5 ohms might mean there’s a problem.
- Test each circuit by disconnecting fuses and measuring current flow. This helps find abnormal current draws or short circuits.
- Use load testing by connecting a test light or bulb to the circuit. This checks the circuit’s integrity under load and finds voltage drops or intermittent issues.
- For advanced diagnostics, use tools like the Load Pro or voltage drop testing equipment. These tools give deeper insights into the wiring system’s health.
Always use the vehicle’s wiring diagrams and manufacturer specs during testing. This ensures you follow the right steps and understand the results. By using these methods, you can check your wiring harness and fix any electrical system problems, keeping your vehicle running well.
Testing Circuit Continuity and Resistance
Checking your wiring harness is key for your electrical system to work right. Testing circuit continuity and resistance is a big part of this. It helps us see if connections are good, find problems, and check the harness’s health.
Measuring Connection Quality
We start with a digital multimeter in continuity mode. This lets us see if there’s a full circuit between two spots. If it works, we hear a beep or see a light, showing the circuit is closed.
Testing each connection, we find any breaks in the electricity flow.
Setting Proper Resistance Thresholds
Then, we check the resistance of the connections. Good connections have a low resistance, about 0.5 ohms (Ω). Bad ones show a high resistance, maybe 1 megohm (MΩ) or more.
Knowing these limits helps us quickly find and fix wire damage and bad connectors.
Identifying Connection Faults
Comparing resistance values to our standards, we find connection problems. Low resistance means a good connection. High resistance means there’s a problem to look into.
This way, we make sure each connection is reliable, keeping your wiring harness in top shape.
Short Circuit Detection Methods
Finding and fixing short circuits in car wiring is key to keeping your vehicle’s electrical system working right. By catching short circuits early, you can avoid problems like blown fuses, tripped circuit breakers, or damaged wires and bad smells.
To spot short circuits, set a minimum isolation resistance of about 1 megohm (MΩ). Test between isolated conductors. Use a digital multimeter or a cable tester to find low-resistance paths. For extra accuracy, use a higher isolation threshold, up to 1 MΩ, for sensitive devices.
Remember these tips when testing for short circuits:
- A low multimeter reading might mean a short circuit.
- Zero volts on a multimeter points to a short circuit.
- An infinite ohms or “OL” reading could mean a tripped circuit breaker or a bad connection.
Fixing short circuits is vital for car wiring diagnostics and electrical system checks. By following these steps, you can keep your vehicle’s electrical system running smoothly.
Advanced Load Testing Techniques
Keeping your vehicle’s electrical system healthy is key. Advanced load testing is a vital part of this. It finds issues that simple tests might miss, like high-resistance connections or intermittent faults. By testing with real-world electrical loads, we can spot problems that could affect your car’s performance and reliability.
Using Test Bulbs for Circuit Verification
Connecting a test bulb or load to the circuit is a good method. It lets us see how the circuit works under real conditions. We use bulbs of different wattages to test various electrical loads, helping us find weak spots in the wiring.
Power and Ground Testing Procedures
It’s crucial to check the voltage and current flow in the harness. We test both power and ground circuits under load. This ensures they work right and helps us find issues like resistance problems or voltage drops.
Using these advanced load testing methods helps us understand your electrical system better. We can fix problems early, keeping your vehicle’s electrical components reliable and efficient. This approach is essential for maintaining your car’s electrical system.
Identifying Intermittent Connection Issues
Fixing electrical problems in a car’s wiring can be tough. These issues often come from changes like temperature, vibration, or bending. These can damage wire insulation and connections.
To find and fix these problems, we use special testers. Tools like CableEye help a lot. They check the wires while we bend and stress them. This way, we can spot small and big issues.
It’s important to test often to catch random problems. This method helps us find issues like wire damage assessment, connector integrity verification, and electrical system troubleshooting challenges.
- Intermittent errors are usually caused by mechanical changes like temperature, vibration, or bending.
- Common causes include bad specs, cold solder joints, and dirty contacts.
- Intermittent shorts can happen when insulating materials fail. Intermittent opens or high-resistance connections can be due to contact or wire issues.
- Micro-fretting, improper mating forces, and poor crimps also cause intermittent problems.
Using advanced testing and a careful approach helps us find and fix these issues. This ensures the electrical systems work well for a long time.
Professional Tips for Wire Harness Inspection
Keeping your vehicle’s electrical system in good shape is key. A detailed wiring harness inspection is essential. Our team at CLOOM Tech offers expert tips to check your wiring harness.
Visual Inspection Guidelines
Begin with a thorough visual check of your wiring harness. Look for any damage like cracks, cuts, or abrasions. Also, watch for corrosion, which can harm electrical connections.
Use tools like magnifying glasses or borescopes for hard-to-see spots. Note any issues you find. These will be crucial for further electrical testing.
Common Problem Areas
- Connection points: Check all connectors and terminals for wear, corrosion, or loose fittings.
- Bends and routing: Look for sharp bends or areas where the harness rubs against other parts.
- Exposure to heat or moisture: Inspect areas exposed to high temperatures or water, as they can deteriorate faster.
Following these steps and fixing any problems, you can avoid serious electrical issues in your vehicle.
Preventive Maintenance and Care
Keeping your vehicle’s electrical system in good shape is key for its performance. To keep your automotive electrics running smoothly, start a detailed preventive maintenance plan for your wiring harnesses. Regular checks and early care can prevent expensive repairs later on.
Begin by checking your wiring harnesses for wear, corrosion, or damage. Clean all electrical connections and use dielectric grease to protect against moisture. Secure any loose wires and replace damaged sections quickly to avoid problems. Keeping maintenance records helps track issues and find systemic problems in your vehicle’s electrical systems.
- Ensure battery voltage is around 12.6 volts when fully charged
- Check that the alternator produces 13.5 to 14.5 volts while the engine is running
- Perform load testing of the electrical system at least twice a year
- Maintain clean, tight, and rust-free ground connections
- Regularly inspect and replace fuses and relays as needed
If you need advanced automotive electrics maintenance or electrical component analysis, get a professional’s help. They have the tools and knowledge to fix any wiring harness issues. Being proactive with maintenance ensures your vehicle’s electrical systems work well for years.
Documentation and Repair Records
Proper documentation is crucial for vehicle electrical repairs. It helps in efficient diagnostics and troubleshooting. Keeping detailed records of all tests, repairs, and replacements is key.
Our approach includes documenting fault codes, test results, and repair steps. We note the parts used, any modifications, and measurements. This helps us understand the vehicle’s electrical system history.
Good documentation aids in future diagnostics and helps spot patterns. It prevents costly breakdowns and ensures the electrical system’s reliability. By documenting thoroughly, we offer top service and peace of mind to our customers.
Common Concerns
What are the basic steps for checking a wiring harness?
First, disconnect both ends of the wiring harness. Then, use a back probe to test. A light bulb helps check for shorts, voltage drops, and circuit integrity. This method saves time by doing multiple tests at once.
What kind of tools do I need for wiring harness testing?
You’ll need digital multimeters, test lights, and special harness testing tools. Always disconnect the battery and wear protective gear for safety.
What are some common wiring harness issues?
Common problems include short circuits, open circuits, and high resistance connections. Symptoms include faulty electrical components, dim lights, and blown fuses.
How do I perform a continuity test on a wiring harness?
Set your multimeter to continuity mode. Check for a complete circuit. Measure resistance to see if connections are good, using thresholds like 0.5 Ω for good connections and 1 MΩ for isolation.
How can I detect short circuits in a wiring harness?
Use a multimeter in resistance mode or a cable tester. Set a minimum isolation resistance threshold (like 1 MΩ). Test between isolated conductors to find any low-resistance paths.
What is the purpose of load testing a wiring harness?
Load testing reveals issues missed by simple continuity tests. Connect a test bulb or load to the circuit. This simulates various loads and can show high-resistance connections or intermittent faults.
How can I identify intermittent connection issues?
Use a tester with fast cycle times and continuous test pulses. Flex connectors and apply stress while monitoring for resistance or continuity changes. Advanced testers can detect both continuity and resistance variations.
What should I look for during a visual inspection of a wiring harness?
Look for physical damage, corrosion, or loose connections. Focus on bends, connection points, and areas exposed to heat or moisture.
How can I maintain my wiring harness?
Start a preventive maintenance program with regular inspections and cleaning. Apply dielectric grease and replace damaged sections. Keep maintenance records to track issues.
Why is it important to document wiring harness tests and repairs?
Documentation helps track recurring issues and aids in future diagnostics. It provides valuable information for technicians working on the vehicle later.